Vol.215 2023年4月号
生産管理DX(デジタルトランスフォーメーション)は、デジタル技術を活用して生産プロセスを最適化し企業の競争力を高めることを目指します。先月はMES(製造実行システム)について紹介しましたが製造工程の様々な情報をデジタル化して管理する上で、RFIDとバーコードは、大きな役割を果たしています。
生産管理DXの必需品:RFIDとバーコード技術の概要
RFID(Radio Frequency IDentification)は、電波を利用して情報を読み取り・書き込みする仕組みです。ICタグには、商品や資材の情報が記録されており、アンテナやリーダライタを用いて情報のやり取りが可能です。
バーコードは、商品や資材に印字されたバーコードを、スキャナで光学的に読み取ることで情報を取得する仕組みです。バーコードは印刷が容易で低コストであることから、多くの業界で広く利用されています。
RFIDとバーコード技術の違いは、以下の点にあります。
通信方式:無線通信を使用し、バーコードは光学的に読み取ります。RFIDは電波を使うので箱の中や裏面からでも読み取りができ、数十~百枚といった一括読み取りも可能ですが、バーコードは一つ一つスキャナで読み取る必要があります。
耐環境性:RFIDは汚れや損傷に対して耐性がありますが、バーコードは印刷面が汚れたり傷ついたりすると読み取りにくくなります。
コスト:RFIDはバーコードに比べ、導入コストが高い傾向があります。
生産管理DXにおいて、RFIDとバーコード技術は、効率化、正確性向上、トレーサビリティの強化などの目的で活用されます。RFIDとバーコード技術を組み合わせることで、互いの長所を活かし、生産管理プロセス全体の効率化と品質向上を図ることが可能となります。以下、代表的な例を紹介します。
製造業バーコード活用例
1 .入出荷検品の効率化と人為的ミス防止
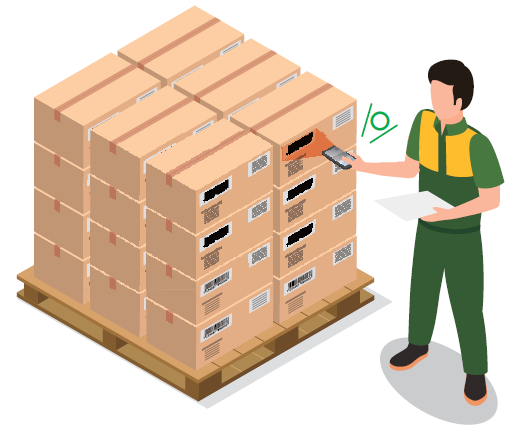
上位システムから入荷予定データを読み込んだハンディターミナルで荷物のバーコードを読み取り、読み取った予定を消し込むことで、正確な入荷状況を把握することができます。
2.工程投入管理の精度向上
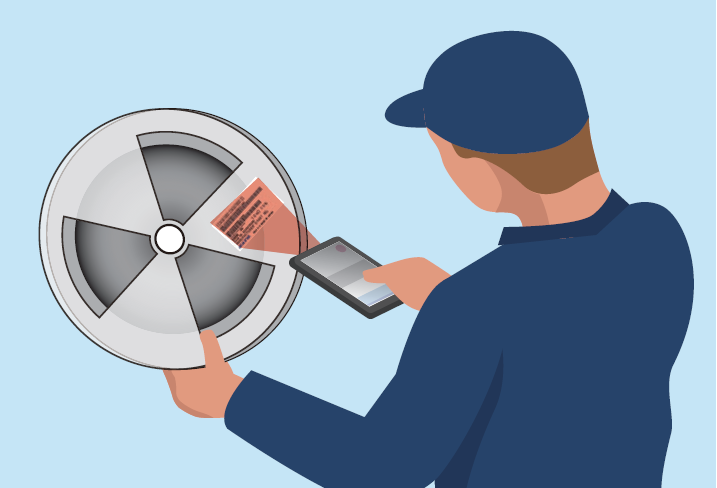
部品や原料にバーコードを付与し、工程投入時のスキャンで誤投入を防ぎ、何がどの工程に投入されたかを正確に管理できるようになります。
3.組み立て工程のミス防止
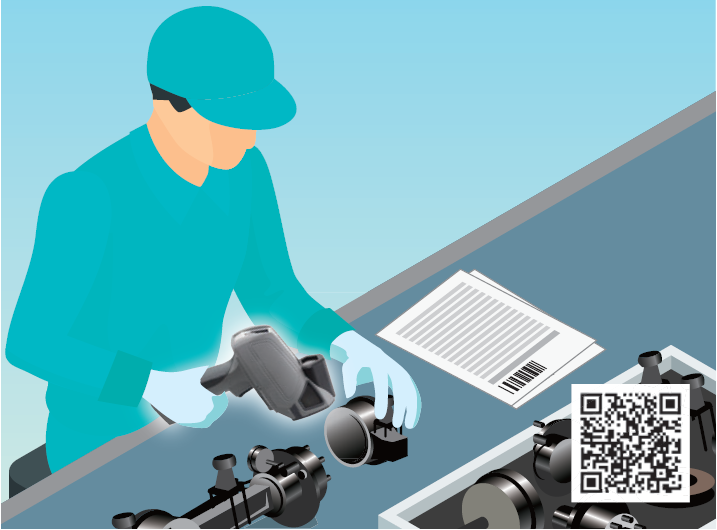
各部品にバーコードを付与し、組み立て工程でハンディ型スキャナを使って指示書と部品のバーコードをスキャンすることで、誤った部品の使用や組み立てミスを防ぐことができます。
4.トレーサビリティ向上
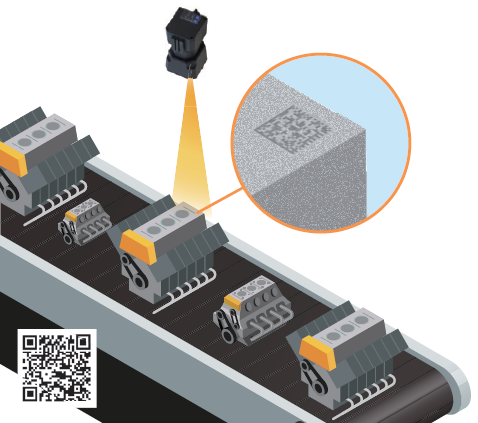
原材料から最終製品までの各段階でバーコードをスキャンすることで、製品の履歴情報を正確かつ迅速に把握できるようになります。RFIDと併用することで、加工実績など詳細な追加情報を書き込むことも効果的です。これにより、部品の製造履歴や検査データを記録し、品質保証や故障原因の特定が容易になります。
製造業RFID活用例
1.入退場管理を効率化
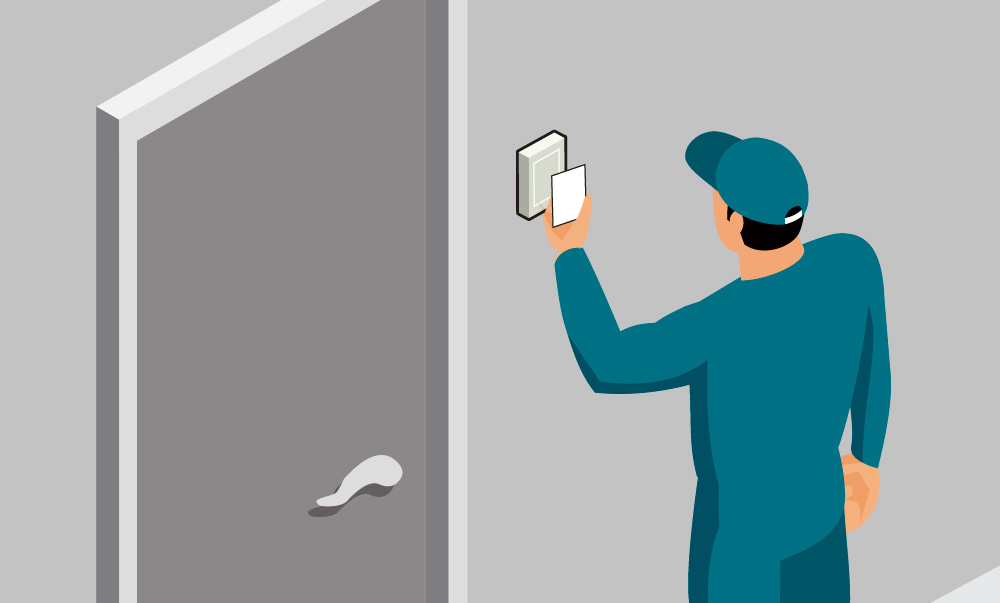
従業員のIDカードや車両などにICタグを取り付けることで、入退出の記録が自動的に管理され、不正アクセスの防止や位置情報管理が効率化されます。
2.入出荷検品の更なる効率化と精度向上
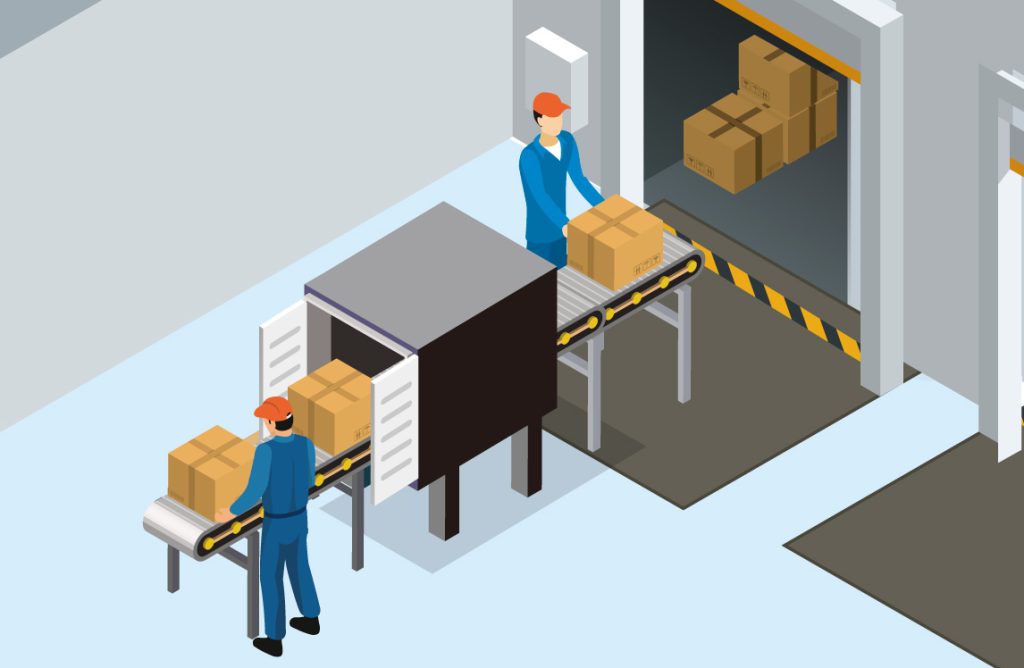
バーコードの場合は一つ一つスキャナで読み取る必要がありますが、UHF帯RFIDの一括読取なら、入出荷の検品作業を自動化することができ、ヒューマンエラーの削減と更なる効率化が実現できます。
3. 在庫管理と所在管理
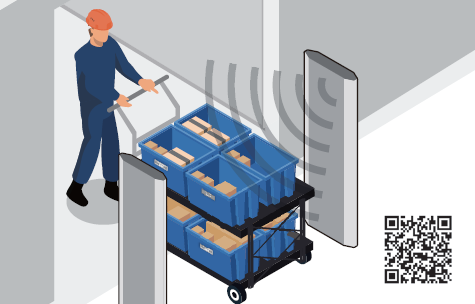
RFIDゲートを通過する際にパレットや、仕掛品に取り付けられたICタグを読みとることで移動実績をリアルタイムで把握することができ、効率的な出庫・製造指示からリードタイムの短縮が期待できます。また、多数のアイテムを同時に検品できるので、ピッキングや棚卸の時間短縮が可能です。
4.作業実績収集の効率と正確性向上
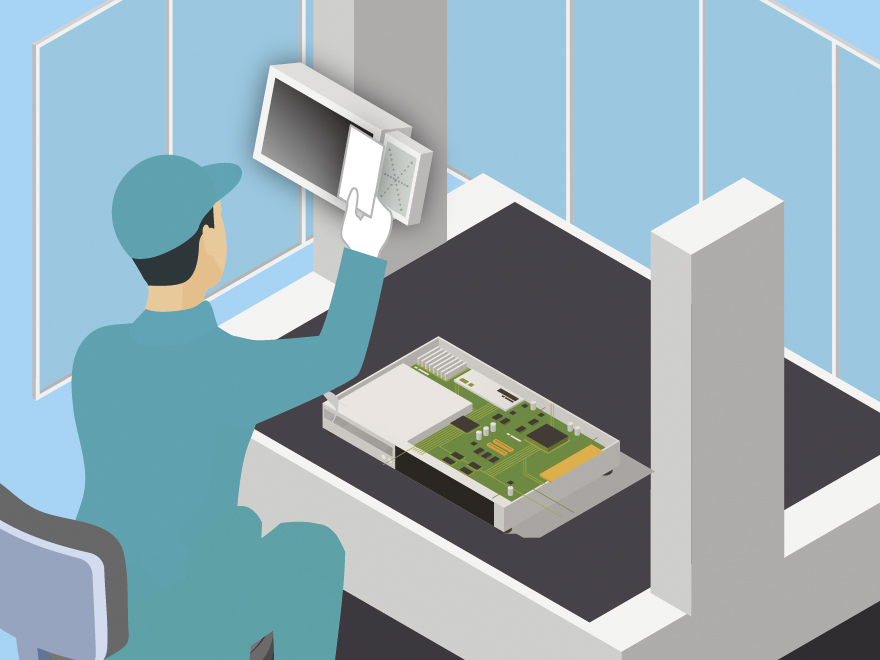
ICタグを作業員のIDカードやカンバンに取り付けることで、作業員が各工程で作業を完了するごとに、RFIDリーダー内蔵タッチパネル端末で実績を収集し、リアルタイムで生産管理システムにフィードバックします。手書きの日報に頼っていた実績収集を自動化できます。
自動認識システム導入のステップ:始めるためのポイント
自動認識システムを導入する際のステップは以下の通りです。
1.目標設定
導入目的・目標の明確化(効率化、コスト削減等)
2.要件定義
機能・性能要件のリスト化(導入に関連する環境や業務フロー、予算に配慮する)
3.技術選定
バーコード、RFID、画像認識等適切な技術の選択(各技術の特
性・コスト・将来性を慎重に比較検討)
4.事前検証・試験導入
システム性能・互換性の確認(試験導入やシミュレーションを行い、問題点や改善点を洗い出す)
5.導入・実装
検証結果に基づく現場への導入・実装(トラブル回避や業務停止を最小限に抑えるために、段階的な導入や適切なタイミングを計画する)
6.教育・研修
従業員への使い方・操作方法の教育と研修(導入効果を最大限に引き出すため、従業員の理解と協力が不可欠です)
7.効果測定・ROI(投資対効果)評価
定期的な効果測定とROIの評価(指標として作業効率、コスト削減、エラー率低減、品質向上など。導入コストと効果を比較し、投資対効果を判断する。)
おわりに
上記活用例のように、自動認識システムの導入により、製造現場での情報収集や活用がスムーズに行われ、上位のMESやERPと連携することで、最適な生産計画や様々な製造工程改善につなげることが可能となります。
当社は長年自動認識システムによる製造業のデジタル化に取り組んできたプロ集団です。ご紹介した以外にも様々な実績がございますので、製造業DX推進にあたって自動認識をご検討の際はお気軽にご相談ください。
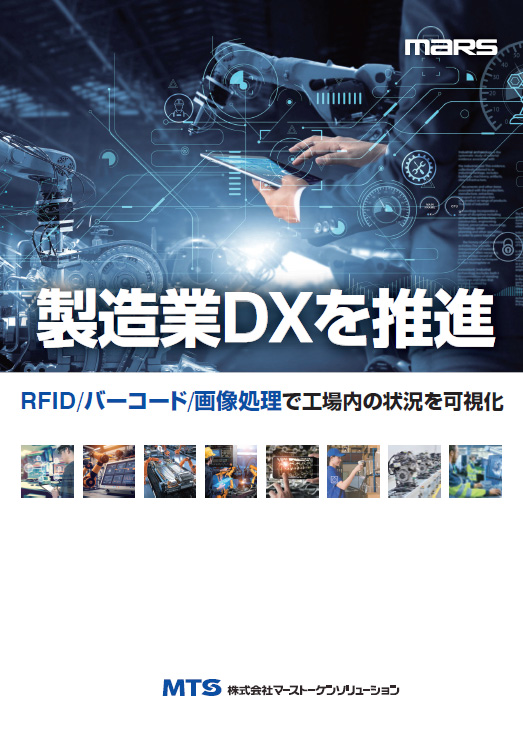
製造業DX推進カタログ
RFID/バーコード/画像処理で工場内の状況を可視化
RFID/バーコード/画像処理で、工場内でのモノと人の動きをリアルタイムでデータ化し、製造業DXを加速させる機器・システムを工程毎に紹介しております。是非ダウンロードしてご覧ください。
- 画像処理で目視による検査判別を自動化
- ICカードタッチパネル端末で実績登録
- 制御PC不要で動作するRFIDリーダライタ
- 誤投入防止と生産実績収集
- UHFフォークで荷物とロケーション情報の登録を自動化
- トラック入退場管理
- RFID一括入荷検品
- Android端末でモバイル検品
- バーコードが無い荷物をOCRで検品&バーコードラベルを発行して個体管理 …他 掲載