VOL.023 flags 2007年3月号
「トレーサビリティ」という言葉が普段の生活の中でも聞かれるようになってから数年が経ちます。 最近ではスーパーの野菜売り場などで生産者の履歴を見ることができるサービスが提供されるようにもなった一方で、 メーカーのずさんな生産管理が問題になる事案もまだ残っています。今回と次回の2度にわたり、 製品事故の未然防止や経営リスクの最小限化の対策として再び注目が集まっている「トレーサビリティ」について解説します。
なぜRSS/合成シンボルが注目されたか
産業界に属するあらゆる企業には、安心・安全な製品を安定的に市場に供給するという社会的責務があります。 原材料の調達から製造、製品の流通販売に至るまで、その品質管理には万全を期す必要があることは言うまでもありません。
企業は製品事故を未然に防止し、経営リスクを最小限に留める取り組みとして”ISO9000″や”HACCP”の認証を取得して、 品質管理に力を注いできていますが、残念ながらこれらのマネージメントシステムを導入しても製品事故に関するニュースは後を絶たちません。 このような事態が企業にどんな影響を与えるのでしょうか。
過去の製品事故を振り返ると、興味深い傾向が見えてきます。 万一の製品事故に備えていた企業とそうでない企業では、製品事故が発生したときに事故による損失とその後のブランドイメージ回復に 対して二極化する傾向が伺えるのです。
テレビのニュースで報道されている記者会見の様子を思い出してください。後々の報道で万一の備えがなかったと判明する企業の多くでは、 発端の情報提供からいかにも手際が悪いという印象を受けます。もちろん記者会見、テレビという大きなメディアに対する不慣れということもありますが 、結果としてメディアや市場からの責任追及が長期に渡って取り沙汰されることで、必要以上に悪いブランドイメージを植えつけてしまうことになります。
さらに製造・品質履歴の不備があったときには、本来、管理していれば必要のなかった範囲まで製品回収を広げることを迫られ、回収判断が遅れることで、回避できるはず の市場への被害がさらに拡大してしまうという最悪のスパイラルに落ちていくというわけです。
一方、万一に備えている企業では、正確・迅速な情報公開と対策をとることができるため、事故が発生してしまった場合でも自らの責任範囲を素早く知らせることができます。 製造履歴や流通経路の特定や回収・撤去といった作業もスムーズに行えるのです。
このような「スピード」が市場に対し被害を最小限に留めるとともに、ブランドイメージを損なうことなく事故を収束させることにつながります。 また、このような「スピード」が企業の高度なリスク管理能力をアピールすることにも繋がり、消費者やユーザーに対してブランドイメージの向上をもたらすケースも少なくありません。 まさに「災い転じて福となす」ことになるのです。
両者の違いはまさしくトレーサビリティシステムの有無の差で、トレーサビリティは企業の存続自体を左右するといっても過言ではないほど重要なリスクマネージメントなのです。
本来、製品事故は起こさないことが大事なのはもちろんですが、人が行っている以上、完全性を求めることも無理があります。「 いかなる対策を講じても製品事故は起こりうる」、「リスクをゼロにすることは不可能なのだ」ということを前提に、製品事故の発生防止に努めつつも、 万一の際に迅速・適切な対応を取るためのリスク管理 ―― トレーサビリティが重要だといえるでしょう。
普及するトレーサビリティ
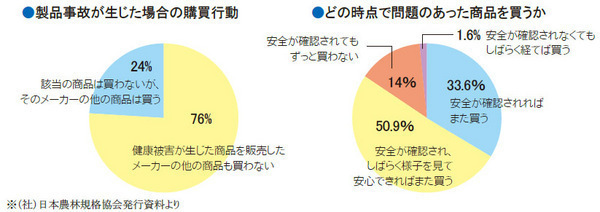
いま、さまざまな企業で「ISO9000」やHACCPといった国際品質規格が取得されています。 これらの規格の中にはトレーサビリティの確立も定義されているので、これらの認証を受けた企業は何らかの手法でトレーサビリティは実現されているわけです。
しかし、最近でも先進的だろうと思われていたメーカーが製品事故に見舞われ、大規模な自主回収に乗り出さなければならなくなるなど、 国際品質規格を取得しているにもかかわらず製品事故が続いています。このような、ある種の矛盾はどうして起こるのでしょうか。 それは認証そのものに「落とし穴」があるからなのです。
さまざまな国際規格では、原材料の使用履歴、製造履歴、品質履歴、流通履歴などを確保するように定義されています。 しかし、どのような手法で実現するかまでは決まりがないことがほとんどで、規格に適合するための方法は各企業に任されています。
製品事故が発生したメーカーのトレーサビリティの仕組みに注目すると、「万一のときのために」ひたすら履歴を蓄積する ―― 履歴の蓄積が主目的になってしまっているケースがあります。現場の作業者も履歴の蓄積作業を強いられているだけで、製品事故 を減らす仕組みが欠けていては本末転倒です。
製造業の重要課題の一つは、事故の起きにくい製品作りの仕組みをいかに構築するかです。製品事故が発生しにくいメーカーは、 製品作りの仕組みがうまく構築されている上で、その副産物としてリスクマネージメントとなるトレーサビリティが構築されているというわけです。
このような仕組みは実際の生産現場が主体となるので、生産効率や不良率を悪化させるようなことはあってはなりません。 また、誰もが確実に作業できなければならないことも言うまでもないことです。 このように予防とリスク管理を兼ね備えたトレーサビリティシステムを構築するためには、システムの根底となる情報と物の流れが正確に連動し、 かつ生きた情報をいかにリアルタイムで収集するかが鍵となってきます。 このような条件にもっとも適しているのがバーコードであり、2次元コードなのです。(次号に続く)