2025年5月号
製造・物流現場でバーコードを確実に読み取るには、印字品質だけでなく「読取環境」を整備・最適化することが重要です。現場ではバーコードの読取不良が生産性低下や誤出荷などのリスクを招きかねません。本稿では、バーコード読取の信頼性向上に寄与するため、「印字」「読取」「検証」3つの要素に沿って基礎知識を整理し、具体的な対策を解説します。
印字フェーズ ―「読める」コードを作る
プリンタ解像度とナローバー幅
ナローバーとは、バーコードの中で最も細いバー(線)の幅を指します。印字が不十分だと読取不能の原因になります。たとえば、203dpiのプリンタでは1ドットが約0.125mmです。理論上は0.19mmの線も出せますが、インクのにじみやヘッドの誤差で潰れやすく、読取エラーが起こりがちです。
そのため、最低でも0.25mm以上のナローバー幅を確保する設計が推奨されます。プリンタの解像度とナローバー幅は密接に関係しており、読取信頼性を左右する基本要素です。
倍率の余裕を持たせる
同じ考え方で倍率にも余裕を持たせます。JAN など一次元コードを 100% から 120% に拡大するだけで、ハンディスキャナが拾える角度と距離の幅が体感で数倍に広がります。二次元コードでもセルサイズを大きくすることで、読取成功率が大幅に向上します。
余白(クワイエットゾーン)の確保
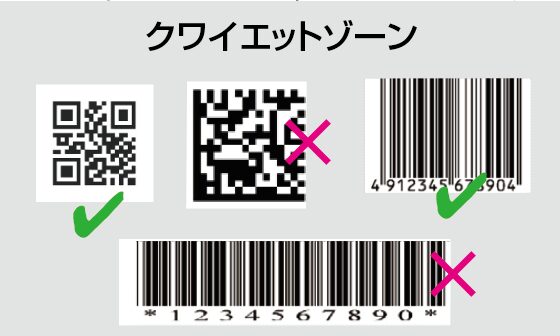
ラベル周囲の余白も重要です。QRコードは四辺にセル4個、DataMatrixはセル1個の余白が規格で定められており、ここに罫線や文字が近づくと品質が低下します。レイアウト段階で白フチを確保し、量産時には版下をロックして余白が削れないようにします。
二次元コードの誤り訂正機能について
QRコードやDataMatrixなどの二次元コードには、『誤り訂正機能(エラーコレクション機能)』が備わっており、一部が汚れたり欠けたりしても正しく読み取れるようになっています。特にQRコードでは最大30%程度の損傷まで補える設定もあり、工場や物流のような過酷な環境で有効です。
ただし、訂正機能を過信せず、印字の鮮明さやクワイエットゾーンの確保など基本設計が良好であることが前提です。訂正レベルは使用環境に応じて選びましょう。
色とコントラストの最適化
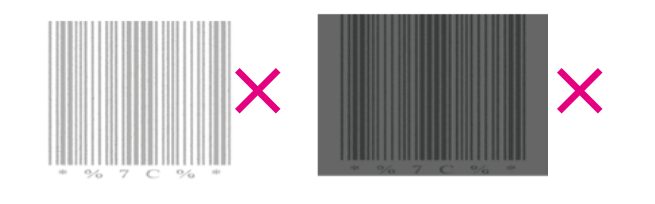
バーと背景のコントラストは、バーを黒・濃紺・濃緑など赤色光を吸収しやすい色にし、背景は白や淡黄など反射性の高い色にするのが基本です。金属や光沢フィルムではレーザーや照明光が鏡面反射しやすいため、マットラミネートや白下地の印刷で反射を抑えます。
印字方式ごとの注意点
印字方式ごとの注意点を確認しましょう。熱転写プリンタは小ロットに適しますが、ヘッドへの粘着剤付着が起きやすいため月次清掃と交換周期の管理が必須です。インクジェットは段ボール等の大面積印字に優れますが、乾燥不足でにじむため、ライン速度やインク種別を変えながら実機試験で最適条件を見つけてください。レーザーマーキングは恒久印字が可能ですが、素材変更で彫刻深さが不足しやすく、洗浄や摩耗で消えることがあるため、材質ごとにパワーとパルス幅を再設定するのが安全策です。
保守と日常点検
保守も重要です。ヘッド温度や印字速度が変わると濃度ムラが出るため、日常的にサンプルを読み取り、異常があれば清掃します。リボンやインクはロット単位で残量を管理し、切れる前に発注タイミングを固定すれば、突発停止を防げます。
読取フェーズ ―「読める環境」を整える
読取方式の適合
バーコードの種類(1次元/2次元)、密度、読取距離に応じて最適なリーダーを選定します。高密度コードには高解像度カメラ式や近接専用機が適します。レーザー式やイメージャ式など方式により得意分野が異なるため、現場業務に合う機種を導入しましょう。また各リーダーには最小バー幅/最小セル(解像限界)があり、自社のコード仕様と合っているか事前確認も必要です。
角度・距離・速度の最適化
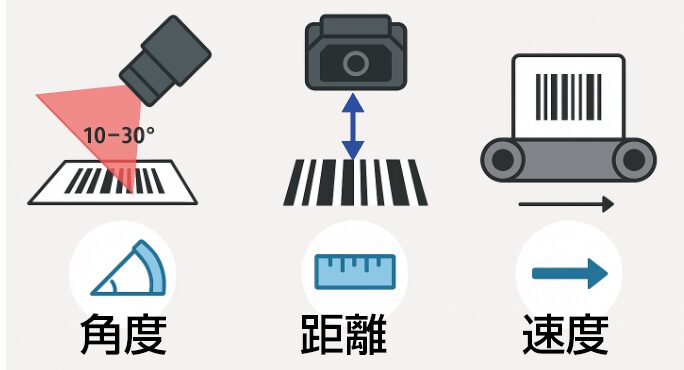
読取精度を左右する三要素は照射角度、焦点距離、対象の移動速度です。
レーザースキャナは 10~30° ほど傾けて照射すると鏡面反射を逃がせます。イメージャは基本的にセンサーに対して正対させると歪みなく撮像できますが、多くの場合、反射を避けるために5~15度ほど傾けて設置した方が安定します。距離は仕様書の被写界深度(DOF)内に合わせ、ライン搬送速度に応じて必要な最大読取速度と露光応答性を備えたモデルを選定することで動体ブレを抑制できます。
照明と外乱光対策
照明や外乱光は読取に影響します。直射日光では反射が飽和し、イメージャが白黒を判別できなくなることがあります。遮光ボックスや偏光フィルタ付きLEDで安定化できます。LEDのちらつきが縞模様になる場合は、DC電源への変更やライン同期で発光を調整すれば改善可能です。
汚損・退色対策
バーコードの汚れや退色も無視できません。油や粉塵がある工程では、あらかじめ透明の耐油ラベルで保護し、糊残りは定期的に除去します。紫外線の強い倉庫ではカラーチェッカで退色を確認し、基準を超えたら貼り替えます。
検証フェーズ ― 品質を数値で担保
検証機とは何か
検証機は、製品トレーサビリティや品質保証が厳しく求められる業界で特に活用されます。医療機器や医薬品、自動車部品、航空機部品、食品・飲料、電子部品など、バーコードの読み取りミスが重大リスクや法規制対応につながる分野で必要性が高いです。
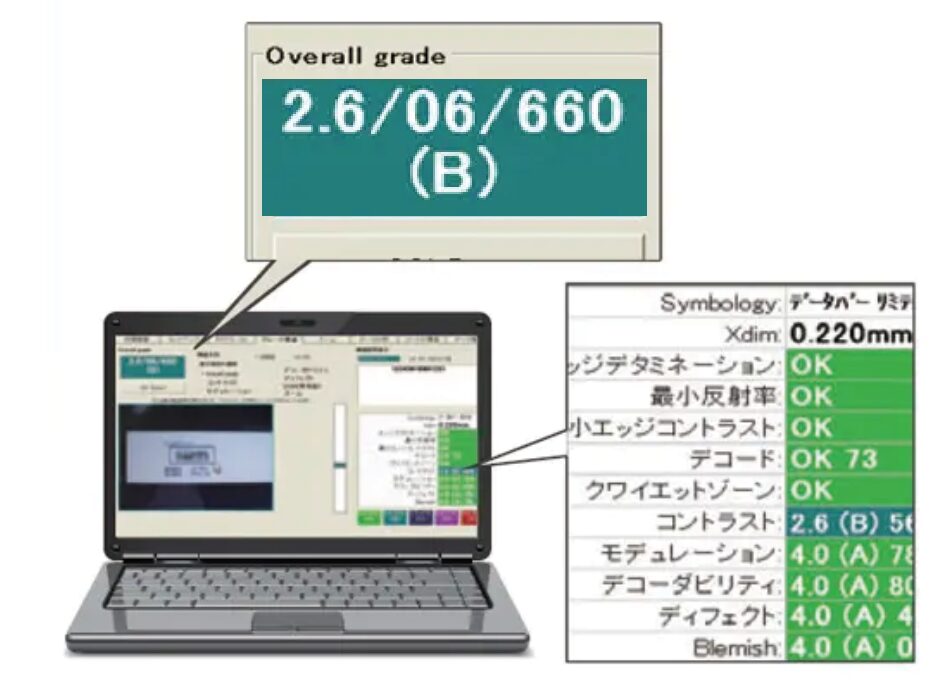
検証機によってISO/IEC15416(1次元)および15415(2次元)準拠で印字品質を評価し、A~Fで採点します。
読み取り成功でもコントラスト不足やモジュレーション不良でD以下になると下流工程や取引先でエラーが増えるため、ロットごとに「C以上」などの基準を設けて検証・判定する運用が推奨されます。
主要検査指標と原因別対策
検証機はコントラスト、モジュレーション、デコード可否、歪みを同時計測します。例えばリボン擦れでバーが薄くなるとコントラスト低下、インク詰まりで太くなるとモジュレーション悪化、貼りズレや熱収縮で台形化すると歪みスコア低下が起きます。レポートに各項目の点数が出るため、改善点を即把握できます。
導入効果とデータ活用
検証機導入で品質データを客観的に蓄積し、取引先提出用資料としても活用可能です。グレード分布から工程能力指数(Cp、Cpk)を算出してPDCAを回しやすくなります。さらに、品番・ロットと検証結果を紐づけて長期保管(5年超)すれば、PL法対応やリコール時のエビデンスとしても機能します。
継続的改善を支える運用フレーム
バーコードシステムの品質は、導入時に整えただけでは維持できません。機器の摩耗や環境の変化、担当者の入れ替わりなど、現場は常に変化します。そこで重要なのが「標準化→教育→点検→改善」の4ステップを回す体制です。
標準化-手順書と基準値の整備
印字設定や読取姿勢、検証基準を文書化し、誰でも同じ操作ができるようにします。「QRコードのセル幅は0.38mm以上」「出荷判定はグレードC以上」など、数値で明確化すると迷いが減ります。手順書は設備や資材の変更時に更新し、共有フォルダや掲示で常に最新版を確認可能にします。
教育と技能維持
標準化した手順を実行するには教育が不可欠です。ハンディスキャナの使い方やプリンタ清掃は、実機を用いたOJTが効果的です。新人に限らず、既存メンバーも半年ごとに技能確認を行い、基準からのズレを防ぎます。
点検サイクル
プリンタやリーダー、検証機の清掃・点検は、日次・週次・月次のサイクルで行います。日常点検では濃度ムラや光量を簡易測定し、週次では清掃を、月例では検証データを集計して品質傾向を確認します。
データ駆動型の改善-PDCA
月例レビューで把握した課題には必ず対策を講じます。「D判定が続くラベルはインク粘度を調整」「読取ミスが多いラインは照明を調整」など、改善後は再検証で数値の向上を確認し、次の課題に進みます。この PDCAを回すことで、品質は着実に向上します。
おわりに
バーコード読取の最適化は、印字・環境・検証のバランスに支えられています。小さな調整の積み重ねが、大きな安定運用につながります。本記事が、現場での読み取り精度向上とトラブル予防の一助となれば幸いです。
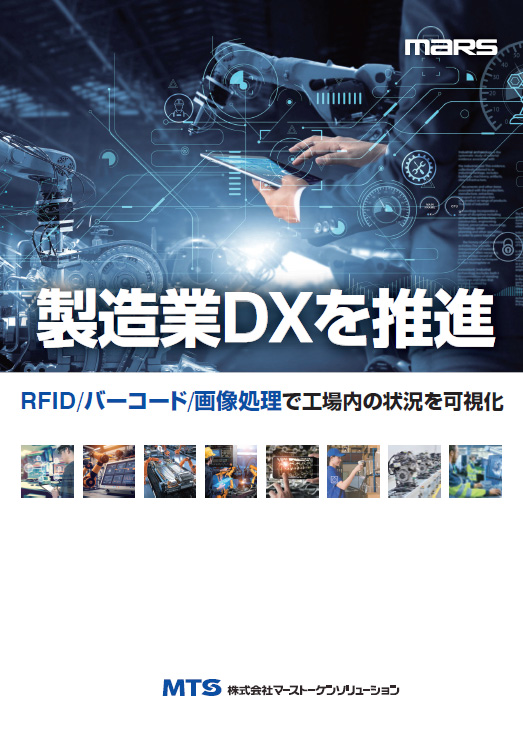
製造業DX推進カタログ
RFID/バーコード/画像処理で工場内の状況を可視化
RFID/バーコード/画像処理で、工場内でのモノと人の動きをリアルタイムでデータ化し、製造業DXを加速させる機器・システムを工程毎に紹介しております。是非ダウンロードしてご覧ください。
- 画像処理で目視による検査判別を自動化
- ICカードタッチパネル端末で実績登録
- 制御PC不要で動作するRFIDリーダライタ
- 誤投入防止と生産実績収集
- UHFフォークで荷物とロケーション情報の登録を自動化
- トラック入退場管理
- RFID一括入荷検品
- Android端末でモバイル検品
- バーコードが無い荷物をOCRで検品&バーコードラベルを発行して個体管理 …他 掲載