VOL.050 2009年6月号
今号の~小分け・誤投入防止システム編~で『食の安心を守る自動認識システム』シリーズも最終号となります。 小分け・投入工程は作業者の能力に依存する部分が非常に多いため、作業ミスは製品事故に直結します。今号ではバーコード・2次元コードを活用した“事故の無い現場システム”を紹介します。
負のスパイラルはこうしておきる
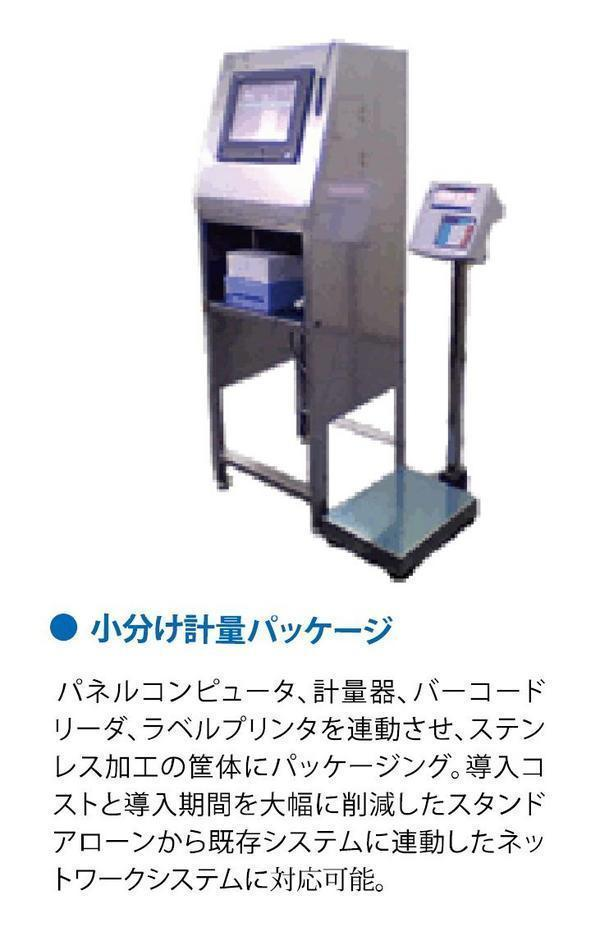
食品加工現場で重要視されていることは、一体何でしょうか?『生産効率』が最 も重要であることは、いうまでもありません。しかしながら、今日この生産効率と同様に重視されているのが、『事故の無い製品作り 』と『製造 履歴管理』(トレーサビリティ)なのです。
実際の現場では、1日に数千個の小分け原料を処理していることも少なくありません。そこでは“数字の読み違い”、“記入間違い”、“原料の取り違い”、“賞味期限切れミス”、“計量許容誤差の精度”、“投入ミス”、“投入漏れ”、“端数原料のムダ”など、現場には数多くの「ミス」や問題 を発生させる要因が絶えず存在しております。
これらを防止するために、何重にもわたる確認(ダブルチェック)が作業として設けられていますが、それでも事故 は起こってしまいます。そして更に事故防止対策として「チェックのためのチェック」という作業が増えることとなり、その結果、生産効率は逆に低下し、更に作業手順がより煩雑になるなどで次 のミスを起こす要因が増加する、いわゆる“負のスパイラル”に落ち込んでいくのが現状です。
また、このような現場に対してリスクマネージメントを目的とした「トレーサビリティ」の導入をむやみに 求めると、前述のチェック機能に加えて、製造履歴を記録する作業負担が増えることになります。これでは現場に対して非常に多くの労力とリスクを求めることになり、先ほどの“負のスパイラル”をさらに 後押しする結果となってしまいます。
では、このような現場で事故の無い製品作りやトレーサビリティを確実 に無理なく導入するにはどうしたらよいのでしょうか?
2次元コードを活用する
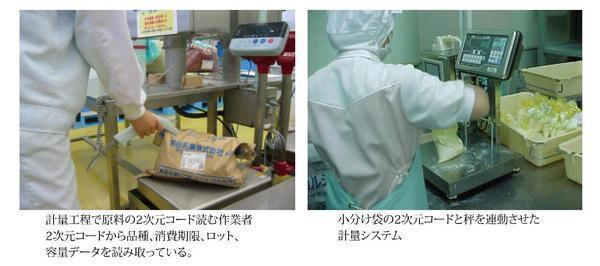
これらの問題を解決すべく登場したのが、すでに数多くの企業で導入されている2次元コードを利用した「現場システム」のです。
まず、原料ラベルに“原料コード”、“ロット番号”、“賞味期限”、“容量”などを2次元コード化(前号参照)して置き、計量・小分け作業時には上記の他に“製造品目”、“容量”、“製造指示日”、“処理バッチ”、“投入順”までを2次元コード化して小分け容器に貼り付けます。 そして原材料の受け入れから投入までの全作業工程で必ず2次元コードを読み取ることで、作業指示や作業の事前チェックが可能なシステムを構築することができます。
2次元コードを利用するメリットは、① 必要な情報をそのままコード化(漢字も2次元コード化することができます。)できること、② 2次元コードを読み取る際、コード化された情報をそのまま作業指示として確認できる点にあります。実際に2次元コードを使用したシステムでは複数作業者によるダブルチェックと台帳記録を廃止して、さらにポカミスや製造ミス撲滅などの大きな成果をあげています。また、これらのシステム導入によって原材料在庫の精度やリアルタイム性が向上し、結果としてキャッシュフローも改善するという2次的な成果も生まれています。
このように全工程に於いて2次元コードを利用し、現場の作業改善をすることにより、必然的に全工程の製造記録がサーバーに蓄積されデータベース化されていくので、自然にトレーサビリティの土台が完成されることになります。