Reasons for introducing the system by client companies
Service providers in railway construction and the production technology department of a certain manufacturing company were visually inspecting the outgoing and incoming tools and measuring equipment, but the large number of items made the checking process time-consuming. They were also looking for a system to prevent tools from being left behind at the site and to manage the maintenance history of the measuring equipment, and were considering RFID tag-based outgoing and incoming management. We were given the opportunity to propose a solution as we can provide a one-stop service from selecting UHF tags to providing hardware, developing systems, and providing installation and adjustment support.
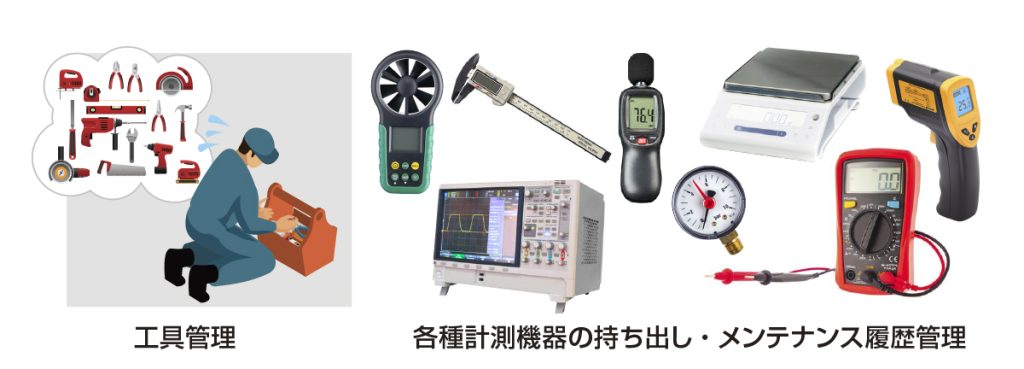
Pre-introduction issues
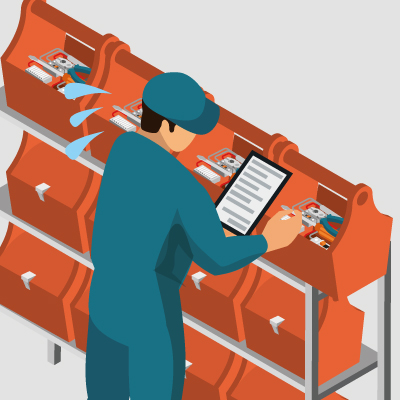
①It takes time and effort to check the borrowing and return information.
It takes time to check tools and fixtures with a large number of management points, which is becoming a burden on field work. They are managed using paper ledgers, but the management of their whereabouts is complicated. As a result, there are problems such as not having enough necessary items when needed and having to spend time searching for them every time.

②Insufficient checking for items left behind at the work site.
Since field work is conducted late at night, there is a risk of overlooking items left behind when relying only on visual checks. As forgetting items at the work site can potentially lead to serious accidents, there is a desire to implement a strict checking system.
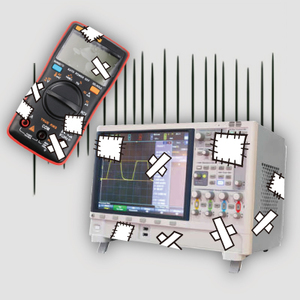
③We want to manage the calibration deadlines for tools and fixtures to prevent malfunctions caused by deterioration.
At the work site, it is difficult to immediately know the purchase date and maintenance history of tools, making it challenging to track which tools have been used how many times and when their calibration deadlines are.
Implemented Solution
System example
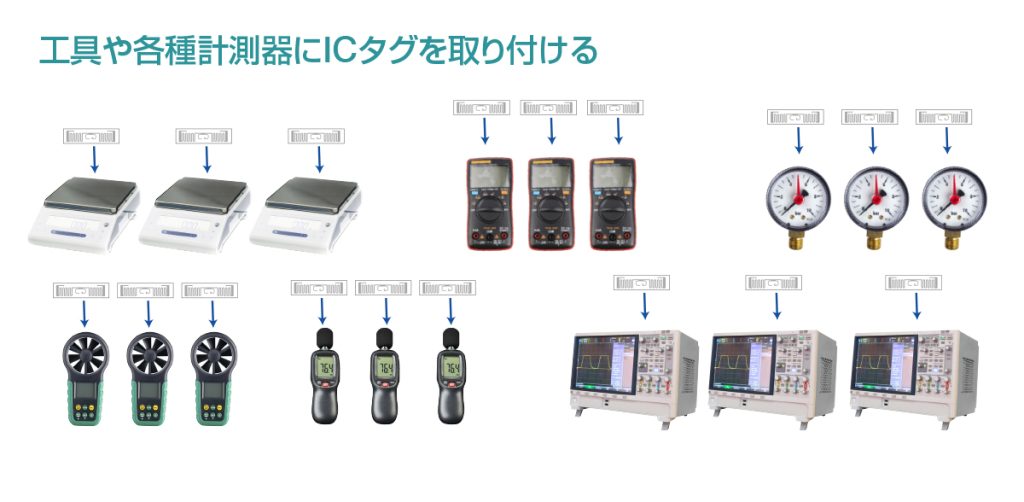
※
※We propose the most suitable tag depending on the item. (We have various types available, such as metal-compatible types and tags that come in different shapes.)
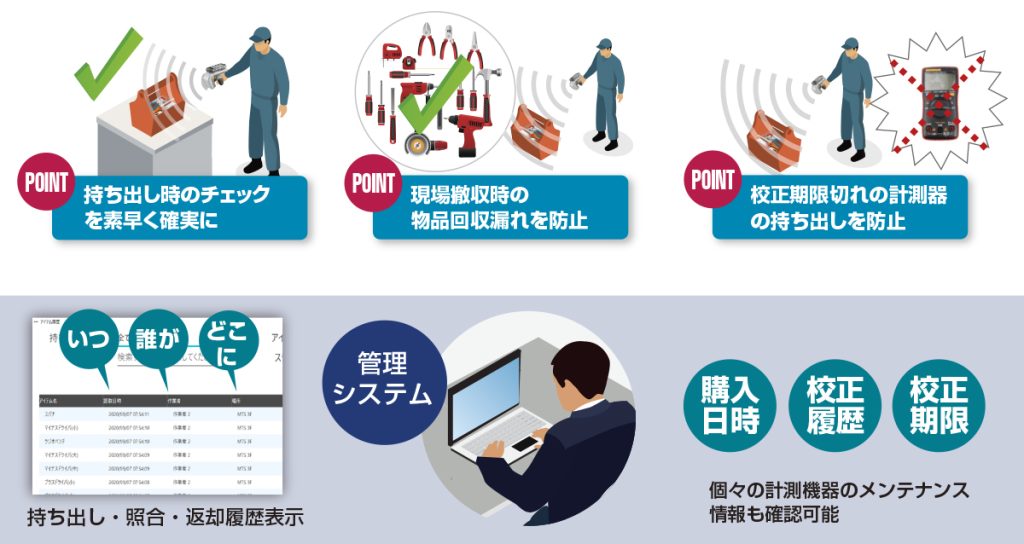
Advantages of implementation
Reduced errors in processing take-outs and returns and increased awareness of the need to manage them as assets
Compared to the days when paper ledgers were used to manage pick/return, the switch to tag reading has reduced human error in the pick/return process.
In addition, workers’ awareness of the need to treat them properly as assets has improved since the tags were applied and strict controls were introduced.
Reducing stress associated with forgetting items at the work site.
By implementing a tag search function for checking forgotten items, it was possible to reduce the workload of workers who were previously straining their eyes to visually confirm items.
Regular inventory checks have been implemented, allowing for quick detection of processing omissions and losses
By attaching RFID tags, the time required for inventory checks has been significantly reduced, enabling monthly inventory checks to be conducted. Additionally, by conducting inventory checks on a short-term basis, oversights in return processing and losses can be quickly detected, allowing for more reliable management of item locations.
Introduction flow
Many RFID installations. You can rely on us.
We have a wealth of information and expertise gained from inspecting many sites.
Based on this, we make the best suggestions for our customers and build a complete technical support system. If you have any questions, no matter how trivial, please do not hesitate to contact us.
MTS pre-introduction consultancy
Introduction flow
- Customer enquiries.
- requirements hearing
- rough estimate
- On-site survey
- Formal quotation
- Equipment and system installation
A team of specialist engineers with extensive local experience will carry out the survey and installation, giving you peace of mind.
- Choice of IC tags and hardware equipment
- System proposals
- Suggestions for site improvements